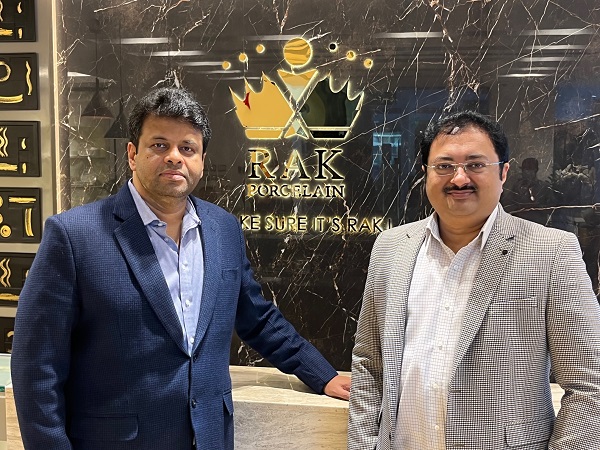
During a recent visit to the United Arab Emirates (UAE), Chronicle.lu got the opportunity to visit the head office and main factories of RAK Porcelain in Ras Al-Khaimah, located around an hour's drive north-east from Dubai, along good roads and through the desert, in the opposite direction from where the World Expo 2020 has been happening.
While Abu Dhabi and Dubai may be the most well-known of the seven emirates, Ras Al-Khaimah (RAK) is starting to get recognition too – Luxair / LuxairTours started to fly there before the pandemic hit. Geographically, the UAE borders Oman to the east and Saudi Arabia to the south and south-west, Qatar and Bahrain are close by to the north-west; the Arabian gulf is to the north.
RAK Ceramics is the 4th largest ceramics producer in the world and is a publicly listed company which started in the UAE in 1989; in 2006, it launched RAK Porcelain Europe in Luxembourg which services the European market and, in 2020, moved its base from Windhof to new premises in Bettembourg (for tableware, clients are solely in the Horeca sector). RAK Porcelain employs 1,300 people in regional sales offices and warehouses at other locations worldwide, including Luxembourg for the European Union and New York for the USA, as well as the rest of the world being serviced from the UAE. RAK Porcelain is currently the 2nd-largest exporter in the UAE.
RAK Ceramics operates four core sectors: tiles (its main business), bathware, porcelain tableware and faucets / taps and has an annual production capacity of 110 million square metres of tiles, five million pieces of sanitaryware, 24 million pieces of porcelain tableware and 600,000 faucets / taps. The company employs around 15,000 people in total, with worldwide sales offices across Europe, India, Bangladesh, Australia, East Africa and Singapore
We were met by Krishna Sajan, Deputy General Manager, and Renu Oommen, Chief Marketing Officer, both originally from India but who have made their career at RAK Ceramics which prides itself on looking after, and retaining, its workforce – more on this later. After admitting that it was great to welcome people to their headquarters and talk with people face-to-face again after soon long due to the pandemic, they recalled the history of the company: after its incorporation into a group in 1989, tile production started in 1991, sanitary ware in 1993 and tableware in 2005.
The company’s main sales drive started in 2006, with Germany the first export market. In Year 1, it had 36 distributors, 64 in Year 2, 90 in Year 3, 120 in Year 4, 136 in Year 5 and currently there are around distributors in 165 different countries in what is a remarkable UAE success story. During this time, production rose from fifteen million pieces a year (40-45k pieces per day) in Year 1 to currently 26 million pieces a year, with the expectation to increase by another ten million within two years.
Being curious about where its raw materials originate (traditionally the UAE sold figs to pay for imports), Renu Oommen explained that while some come from the UAE itself, many come from France and Germany (decoration materials) and also the United Kingdom (China clay). The only out-sourced production concerns cutlery which is made in Vietnam.
On a tour of the showrooms, we learnt that 3D printing is being used more and more in certain areas of the production process. Its factories are all located in the same area and comprise three million square metres. The personal guided tour included RAKstone, ivory porcelain, white porcelain, bone China (new), fusion (colour glaze) and glassware, as well as cutlery.
The guided tour continued with a drive through one of the factories, a single 65,000 m2 single-storey building. All storage is open as, before packaging, everything is cleaned due to the sand / dust from the desert that gets everywhere. Here, we learnt that 25,000 pieces get decorated daily: here they use roller kiln technology, not tunnel kilns; the biscuit kiln is used three times for decorated plates.
The corporate / administrative language used in the company is English, yet 80% of the workforce is Indian (Hindi and other languages are spoken between workers on the factory floor). The staff canteen and tea / snack trolleys cater for Indian, Filipino and African cuisine. Staff accommodation is provided, with a medical centre on site. It is so large that most people use bicycles to get around and between the factories. Staff also get one month vacation a year and a ticket home for themselves and their family.