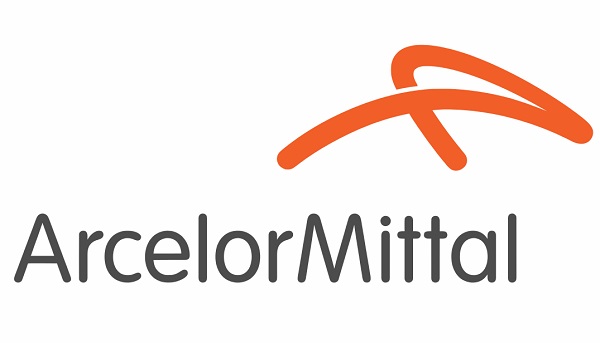
Arcelor Mittal recently provided updates on its strategy to invest in lower-carbon “hydrogen-ready” DRI-EAF facilities as a key step in replacing several blast furnaces across its European operations to reduce emissions.
These projects have received funding support from host countries, approved by the European Commission.
The investments were based on favourable policy, technological and market conditions to offset the higher capital and operating costs of decarbonisation. This included the ability to use natural gas as a transition fuel until green hydrogen became cost-competitive.
However, ArcelorMittal noted that European policy, energy and market environments have not evolved as expected. Green hydrogen remains far from being a viable fuel source, and natural gas-based DRI production in Europe is not yet competitive as an interim solution. The company also highlighted weaknesses in the Carbon Border Adjustment Mechanism (CBAM), insufficient trade protections against increased imports due to China’s overcapacity, and limited customer willingness to pay premiums for low-carbon steel.
Before taking final investment decisions, Arcelor Mittal stressed the need for full visibility on clear policy frameworks to ensure higher cost steelmaking can be competitive in Europe without a global carbon price. Key developments expected in 2025 include the CBAM review, updates to steel safeguards and the Steel and Metals Action Plan, which are anticipated to shape the business case for decarbonisation.
In the meantime, the company continues engineering work, as well as analysing a phased approach that would start with constructing Electric Arc Furnaces (EAFs) capable of processing scrap steel to significantly reduce emissions.
In May, ArcelorMittal began constructing a 1.1 million-tonne EAF at its Gijón, Spain plant, expected to cut CO2 emissions by 1 million tonnes. They also reported progress at their Sestao, Spain plant, targeting an increase in production to 1.6 million tonnes by 2026, largely comprising XCarb® low-carbon steel. ArcelorMittal emphasised its market leadership in XCarb® sales, achieving a carbon footprint as low as 300kg per tonne and expects to double sales to approximately 400,000 tonnes this year.
The company stated that the extended timeline for final investment decisions will not impact its ability to meet demand for low-carbon steel, as the Sestao revamp project will enhance its flat product production capacity. Any revision to the current 2030 intensity targets will be set out in the forthcoming Climate Action Report 3. ArcelorMittal also highlighted a 28.2% reduction in absolute emissions across its European operations since 2018, largely due to lower production amid weak demand.
Longer term, ArcelorMittal confirmed that it remains committed to all technologies that offer the potential to take steelmaking to near-zero. This includes carbon capture utilisation and storage (CCUS), although like green hydrogen, this technology is likely to only play a significant role after 2030. It already has one industrial scale CCU facility operational at its plant in Gent, Belgium, and a further two pilot projects underway in Gent.
Aditya Mittal, Chief Executive of ArcelorMittal, commented: “ArcelorMittal remains absolutely committed to decarbonisation. It is the right thing to do, both for the company and the planet. I remain confident that we can still achieve our net-zero by 2050 target, but the shape of how we will achieve this could differ from what was previously announced. (...) I hope to see new policies coming into play that will support an accelerated transition. The Green Deal Industrial Plan and the Steel and Metals Action Plan, and the legislation flowing from them, will be important, as well as regulation to stimulate the demand signal. While we do have customers that want low-carbon steel, those that do and are willing to pay a premium are still very much in the minority. I expect policy decisions taken in 2025 will help bring clarity on how we will move forward to decarbonise our assets, taking advantage of our unique global profile, superior technology and raw materials mix and industry leading innovation.”