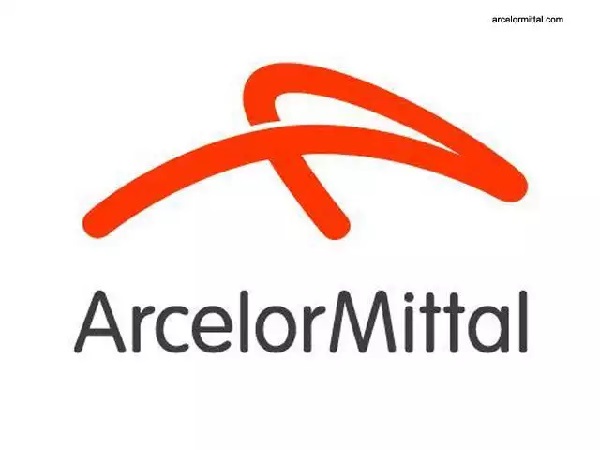
ArcelorMittal Europe has announced its decision to reduce carbon emissions by 30% by 2030, in its efforts to contribute to the European Commission’s Green Deal.
In its CO2 roadmap, ArcelorMittal Europe – Flat Products has set this target in line with its earlier announced ambition (in May) to be carbon neutral in Europe by 2050.
The roadmap to achieve the 30% target is based on three distinct pathways that have the potential to deliver a significant reduction in carbon emissions, including: clean power steelmaking, using clean power as the energy source for hydrogen-based steelmaking and longer term for direct electrolysis steelmaking; circular carbon steelmaking, which uses circular carbon energy sources, such as waste biomass, to displace fossil fuels in steelmaking, thereby enabling low-emissions steelmaking; fossil fuel carbon capture and storage, where the current method of steel production is maintained but the carbon is then captured and stored or re-used rather than emitted into the atmosphere.
Considered key to the success of both the roadmap and ArcelorMittal Europe’s ambition to be carbon neutral by 2050 will be supportive policy to ensure a global level playing field. Consequently, ArcelorMittal has confirmed its support of the European Commission’s Green Deal, as well as its belief that the right market mechanisms are a critical part of enabling the deployment of low-emissions steelmaking. This includes a carbon border adjustment complementary to the existing ETS and the Just Transition Fund, to invest in research, innovation and green technology.
Initiatives and technologies underway or to be implemented at ArcelorMittal Europe – Flat Products’ different sites include:
- Carbalyst – capture waste gases from the blast furnace and biologically convert it into bio-ethanol. The €120 million launch project at ArcelorMittal Ghent is expected to be completed in 2020;
- IGAR – captures waste CO2 from the blast furnace and converts it into a synthetic gas that can be reinjected into the blast furnace in place of fossil fuels to reduce iron ore. An industrial pilot of this technology is being developed at ArcelorMittal Dunkirk in France;
- Torero – €40 million investment to convert waste wood into bio-coal to displace the fossil fuel coal currently injected into the blast furnace. The company's first large scale demonstration plant in ArcelorMittal Ghent is expected to be in operation by the end of 2020;
- Reducing iron ore with hydrogen – €65 million investment at Hamburg site to increase the use of hydrogen for the direct reduction of iron ore;
- Carbon capture and storage – integrating breakthrough technologies to bring down the costs of capturing, purifying and liquifying CO2 from waste gases. Construction of a carbon capture and storage pilot project, 3D, will begin at ArcelorMittal Dunkirk in 2020 and will be able to capture 0.5 metric tons of CO2 an hour from steelmaking gases by 2021.
Geert Van Poelvoorde, CEO ArcelorMittal Europe – Flat Products, commented: “We are committed to the decarbonisation of the steel industry, in line with the objectives of the Paris Agreement and the European Union’s commitment to net-zero by 2050 as announced in the Green Deal [last] week. Our roadmap and the emissions reduction target of 30% by 2030 for Europe is a big step in the right direction. It’s not a one-size-fits-all model, as different parts of our business are at varying starting points".
He added: "For some sites, certain technologies will work while others will be suited to another route. We’ve spent the last few years testing a range of technologies and now is the time to scale up and put them into action, with the support of the EU and member states, to ensure we are able to fully decarbonise”.