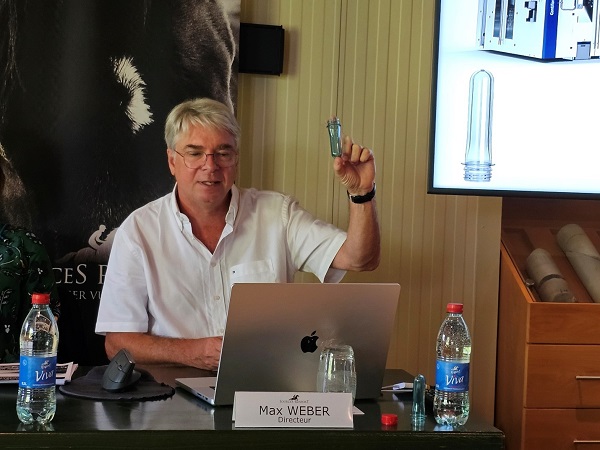
On Thursday 19 September 2024, at a press conference at its offices in Rosport, the eponymous mineral water company unveiled its response to the EU directive 2019/204 on single-use plastic products.
Among other things, the directive imposes a cap tethering system on plastic bottles with a view to preventing the caps from being discarded separately into the environment, and requires that, from 2025, PET (Polyethylene Terephthalate) beverage bottles must “contain at least 25% recycled plastic as an average of all PET bottles placed on the market on the territory of that Member State” (30% from 2030).
There was a 3 July 2024 deadline imposed for the mandatory introduction of bottle cap tethering, and, in the knowledge that the directive already implied a change in certain processes, Sources Rosport took the opportunity to revisit its entire bottle production strategy. The aim was not only to comply with the directive, but also to achieve a significant reduction in transportation costs (and associated greenhouse emissions) and to leverage its highly localised marketing strategy (it does not export outside Luxembourg) in order to get as close as possible to what the EU directive describes as “a circular life cycle for plastics” in the context of single-use beverage bottles.
In parallel with the need to comply with the directive, Rosport noted that its bottle production could be optimised. Although the bottles and caps are produced in Luxembourg, along with the labelling and some packaging, the company was shipping nearly half a million pre-made PET bottles from Plastipak in Bascharage to Rosport per week, of which the overwhelming content was air.
The company has thus invested some €2 million in installing its own high performance bottle air-moulding facility, and now, instead of those 17.5 trucks, a single truck full of pre-forms is shipped in per week (a round trip of 128 km is required per truck for delivery and return). These preforms go through a process of heating to 130° and then inflating into two piece moulds at a pressure of 35 bar, a little like glass blowing.
Additionally, Sources Rosport has rationalised its bottle range. They are now all transparent and, for any given capacity, are useable for any of its water products.
As far as the circular life of the bottle is concerned, all the preforms are made of recycled PET, and are, in turn, 100% recyclable themselves, thus already far exceeding all foreseen EU requirements. This is made particularly achievable by Rosport’s deliberate policy of only supplying within the borders of the Grand Duchy, and therefore, through the 2014 agreement signed with Valorlux and Plastipak, used bottles are able to be selectively recycled and used for the production of new bottles (bottle to bottle). Continuing with the policy of working with local suppliers, the caps are supplied from Wiltz, the labels are printed in Fridhaff, and the cardboard for the trays and pallet inserts comes from Lintgen.
In order that transparency is not confined only to its new bottles, Sources Rosport has added a new traceability section to its website in order to allow interested consumers to be able to follow the journey of its products. More information on this and the whole process can be found through the English-language press release issued on 19 September by Rosport.
(Pictured: Bottle preforms and mould. The screwtop section is already a part of the piece so that the high pressure airline can be attached to inflate the heated preform into the mould.)