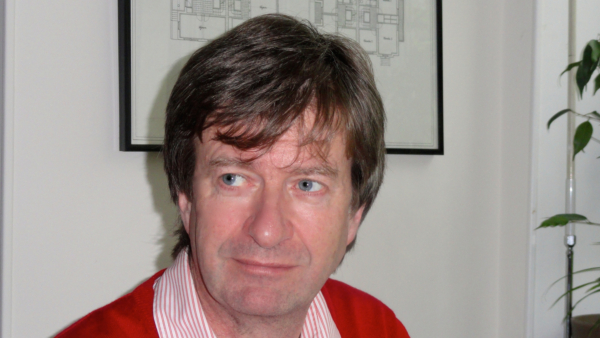
Chronicle.lu recently got the opportunity to speak with Colum Mulhern, architect and owner of Colum Mulhern Architecte, about supply chain shortages and recent price increases in construction materials and how these have impacted family house business and transformative works.
Colum Mulhern arrived in Luxembourg in November 1984, just after finishing architectural school in the United Kingdom. He has been practising exclusively contemporary classical and traditional architecture since setting up his own firm in early 1989. He argues that the most widely used modernist style of architecture fails to produce pleasant places for people to live.
Chronicle.lu: Has classical and traditional architecture been impacted by supply chain shortages in construction materials?
Colum Mulhern: All building, classical and modernist, has been impacted by supply chain shortages recently, particularly since the beginning of the pandemic which affected the production of materials. And since virtually all building materials used in Luxembourg are imported, there were added problems with transport during periods of lockdown.
Renovation projects were probably less affected by the delivery of materials during the COVID-19 public health measures, as they are more labour intensive and less dependent on materials.
Heritage protection is therefore very important if we are trying to create a more sustainable world. According to the Guardian, the renovation of a historic building consumes around 7% of the energy required to demolish and build the same volume.
Chronicle.lu: Which construction materials have been most impacted, in terms of volume, availability and prices?
Colum Mulhern: Almost all materials were affected to some extent as lockdowns first hit production chains as factories were closed. As stocks depleted, prices rose as the highest bidders were supplied first. Some materials were affected in ways we could never have imagined. For example, the production of KG2000 drainpipes which are used for buried wastepipes as well as in housebuilding, were stopped soon after the aviation industry ground to a halt. The raw material used to make these pipes is a by-product of the production of aviation-kerosene for airplanes. When the need for kerosene dropped significantly during the pandemic, the supply of the raw material used to make the pipes also fell to zero.
At one stage, even the electricity cables were no longer available. Thankfully, things seem to be moving again and prices seem to be coming back down from their highs.
Chronicle.lu: Did you notice price increases in roofing material and wood in particular, and how has this impacted your current projects?
Colum Mulhern: Timber has been probably the hardest hit by price rises and supply shortages. Recent years have seen an increase in demand for wood as people think that building in wood is an act of sustainability. More wood is also required for building of traditional roofs as the ever-increasing thickness of insulation demanded by building regulations means deeper roof joists and added weight to traditional roofs. But surely cutting down trees is the least sustainable act one can do, so in many ways increasing insulation thicknesses has been counterproductive. Even managed forests take time to replenish stocks of wood as it takes decades and even more than a century for some trees to reach maturity.
Lately, disease has been ravaging wood stocks in North America, and as production has also slowed in Russia to protect their own natural resources, the United States (US) has been forced to look elsewhere to supply timber to its own local market. Last year, the US entered the European market, where China is already very active, to buy wood for the US building industry, pushing prices beyond what many local sawmills could afford. Prices more than doubled and delivery time went from two weeks to five months at one point. Roofers and suppliers in Luxembourg were getting price increases every two weeks instead of every year.
China has already been buying up European oak at inflated prices which local firms can’t afford and make parquet, which they sell back to the European market. The transport of huge volumes of wood in both directions where the end user is in the same part of the world where the trees grow is an absurdity of globalisation.
Chronicle.lu: How many of your current projects have been delayed due to material shortages?
Colum Mulhern: All of my current projects on site have been delayed, but more because of COVID-19 restrictions than material shortages. People in contact with those testing positive have had to remain in quarantine, leading to teams disappearing from building sites. This also meant replanning everything.
Some firms organised their building sites according to the deliveries they received rather than the dates they received the orders, but as children in quarantine had to be cared for at home, many workers on building sites had to stay back as well to care after them. With many changing factors coming from multiple directions, this meant that firms had little idea how to organise work on the contracts they had. At the beginning of 2021, many firms refused to participate in tender actions. Many firms couldn't take on any more work in the next twelve months.
Many projects in the design and authorisation stages were also slowed down when clients took more time to think as they saw prices rise, particularly in wooden construction. Many projects to be built in wood were shelved when budgets almost doubled.
Chronicle.lu: Apart from construction material, did you have any other shortages, like equipment and how has this impacted your projects?
Colum Mulhern: I didn’t notice any problems with equipment shortages yet.